OI France Veauche
Le leader mondial de l’emballage en verre Owens Illinois possède 9 verreries en France. Certains sites sont spécialisés dans la production de bocaux. Le site de Veauche, où sont employés 290 personnes, produit exclusivement des bouteilles. La verrerie devant tourner 24h/24, les employés fonctionnent en 5/8, c’est à dire que 5 équipes se relaient en permanence pour assurer la production. Chaque équipe travaille 8 heures d’affilée.
La verrerie OI France de Veauches a été fondée en 1883 à la demande de Badoit qui avait besoin d’une verrerie proche d’une ligne de chemin de fer pour conditionner l’eau minérale qu’elle produisait. De nos jours, l’eau minérale Badoit étant conditionnée essentiellement en bouteilles en plastique, la verrerie s’est tournée vers de nouveaux clients qui cherchent des bouteilles en verre pour leur produits. La verrerie produit chaque année 330 millions de bouteilles. Elle peut produire plus de 600 modèles de bouteilles différentes, de la petite bouteille de Cognac à la grande bouteille de 3 litres.
Un des avantage de l’emballage en verre est qu’il est recyclable à l’infini. Une bouteille en verre de teinte « chêne » peut comporter jusqu’à 90% de verre recyclé.
Une bouteille en verre blanc comportera 75% de verre recyclé et demandera plus d’énergie pour être réalisée.
Visite du site de production
Jean-Paul Montchamp (Fondeur à la retraite) et Philippe Mouton (Electrotechnicien à la retraite), nous ont fait visiter la verrerie et nous ont expliqué en détail le fonctionnement du procédé de fabrication.
Les fours
Pour fabriquer les bouteilles, tout part de deux immenses fours dans lesquels 400 tonnes d’un mélange de sable, de carbonate de soude et de calcaire sont portés à 1550°C. Cette température, bien que très élevée, est contrôlée au degré près, et le niveau du verre fondu dans le four est réglé au centième de millimètre.
A ce mélange en fusion, on rajoute des additifs qui permettront de définir précisément la couleur du verre : Phonolite, dolomie, feldspath, alumine, sulfate, ou coke. Le verre sort du four par un siphon, qui alimente des canaux appelés feeder. Le verre peut-être refroidit sur les feeders afin d’atteindre le température souhaitée au moulage : 1100°C. En bout du feeder, deux gouttes appelées paraisons se forment. Ces gouttes tombent dans le moule ébaucheur, puis l’ébauche est retournée et introduite dans le moule finisseur. Là, de l’air comprimé est injecté, ce qui vient plaquer le verre contre les parois du moule. La bouteille ainsi formée est extraite du moule et part sur un tapis roulant.
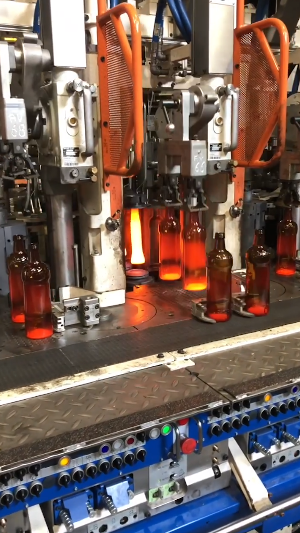
Il est indispensable de graisser régulièrement le moule, sinon le verre s’accroche au métal. On vient même graisser la paraison pour qu’elle tombe le plus vite possible dans le moule ébaucheur. La vitesse est essentielle pour que la paraison tombe bien au fond du moule ébaucheur où se forme le goulot.
A la sortie du moulage, un soufflage refroidit le verre pour le solidifier. Les bouteilles sont alors à 500°C.
Elles passent ensuite dans un four tunnel appelé arche de recuisson. Les bouteilles rentrent à 500°C et la température remonte à 540°C, pour baisser progressivement jusqu’à 90°C en sortie de l’arche. Le but de ce traitement thermique et d’éliminer la plupart des tensions qui sont apparues lors du moulage. Sans cela les bouteilles seraient extrêmement cassantes et dangereuses pour les utilisateurs.
La chaîne de conditionnement
Les bouteilles subissent ensuite un traitement de surface. On vaporise à l’extérieur des bouteilles encore chaudes un produit qui évite qu’elle ne se rayent par la suite en frottant les unes contre les autres.
Elles sont ensuite contrôlées. Les contrôles concernent la présence de bulles d’air dans le verre, ou de fêlures. On contrôle aussi la forme de la bouteille. Ces contrôles peuvent être réalisés en utilisant des techniques très variées :
• contrôle mécanique par palpeurs,
• contrôle optique par laser,
• contrôle par injection d’air comprimé pour vérifier la présence de fêlures au niveau du goulot,
• Imagerie et reconnaissance de forme.
Enfin un contrôle humain peut être réalisé pour les bouteilles à forte valeur ajoutée. Les bouteilles qui présentent des défauts sont éjectées et renvoyées vers le four de fusion du verre, où elle participeront à la formation de nouvelles bouteilles.
En fin de la ligne de contrôle, les bouteilles sont retournées et soufflées pour vérifier qu’aucun corps étranger ne se trouve à l’intérieur.
Elles sont ensuite regroupées en couches à l’aide d’un orienteur puis regroupées en plusieurs couches superposées à l’aide d’un palettiseur. La chaîne d’emballage la plus récente est équipée d’un grand bras robotisé de marque Kuka, qui effectue le même travail à des cadences supérieures. La palette ainsi formée est enrobée d’un film plastique et envoyée à l’expédition.
En septembre 2021, OI France a inauguré un nouveau four pour la verrerie. L’investissement correspondant s’élève à 30 millions d’euros, ce qui prouve que cette industrie comptera à l’avenir.